Ключевое различие между PFMEA и DFMEA заключается в том, что PFMEA помогает анализировать потенциальные сбои конкретного процесса бизнес-подразделения, тогда как DFMEA помогает анализировать потенциальные сбои дизайна продукта.
Метод FMEA (анализ последствий режима отказа) помогает определить потенциальные режимы отказа процесса при управлении операциями и дизайне на этапе разработки продукта в системе и классифицировать отказы на основе вероятности и серьезности отказа. Режим отказа относится к любым дефектам или ошибкам в конструкции, процессе или элементе, которые влияют на клиента. «Анализ последствий» относится к изучению последствий сбоев.
Что такое PFMEA?
PFMEA расшифровывается как анализ эффектов режима сбоя процесса. Эта методология может определить потенциальные режимы отказа в процессах на уровне эксплуатации. Как правило, технически опытная команда проводит PFMEA. Основной процесс заключается в сборе адекватных данных о причинах режимов отказа для устранения или минимизации последствий режима отказа.
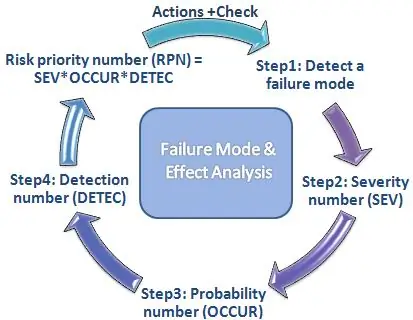
Кроме того, PFMEA - это структурированный инструмент, используемый всеми видами организаций. Он помогает формировать последствия режимов отказа и расставляет приоритеты в действиях, необходимых для снижения риска. PFMEA документируется и представляется перед запуском любых новых процессов для снижения потенциальных опасностей. Кроме того, это также возможно применить к преобладающим процессам, чтобы добиться постоянного улучшения системы.
Что такое DFMEA?
DFMEA расшифровывается как Анализ последствий режима отказа конструкции. Эта методология помогает выявлять потенциальные сбои в конструкции продукта на стадии разработки. В большинстве случаев инженеры используют это как процедуру для изучения возможности отказа конструкции в реальной ситуации или использовании.
Основным инструментом DFMEA для инженеров является матрица DFMEA. Эта матрица представляет собой структуру для сбора и документирования связанной информации, включая технические спецификации, даты выпуска, даты пересмотра и членов группы. Как правило, DFMEA - это совместная работа технических специалистов и, возможно, межфункциональной команды. Более того, DFMEA не полагается на средства управления технологическим процессом для преодоления возможных ошибок конструкции
Каковы сходства между PFMEA и DFMEA?
- PFMEA и DFMEA - это два типа анализа эффектов режима отказа.
- Основные шаги в DFMEA и PFMEA похожи, но они имеют два разных применения.
- И DFMEA, и PFMEA указывают на возможные сбои, серьезность рисков, существующие средства контроля, рекомендации и улучшения после рекомендуемых действий.
- Конечной целью обоих является сокращение или предотвращение крупных упущений в продуктах и производстве.
- Эти методологии также могут снизить стоимость проектирования или эксплуатации.
- Кроме того, некоторые сбои не могут быть устранены на DFMEA. Эти отказы могут быть переданы в PFMEA для принятия необходимых мер по улучшению продукта.
В чем разница между PFMEA и DFMEA?
Основное различие между PFMEA и DFMEA заключается в том, что PFMEA включает в себя процессы, в то время как DFMEA включает дизайн продукта. Основная цель DFMEA - выявить потенциальные сбои в конструкции продукта, тогда как основная цель PFMEA - выявить потенциальные сбои процессов. Базовый обзор DFMEA проводится с использованием схемы продукта, в то время как PFMEA проводится с использованием блок-схемы процесса. Еще одно различие между PFMEA и DFMEA заключается в том, что PFMEA происходит на операционном уровне, тогда как DFMEA происходит на этапе разработки.
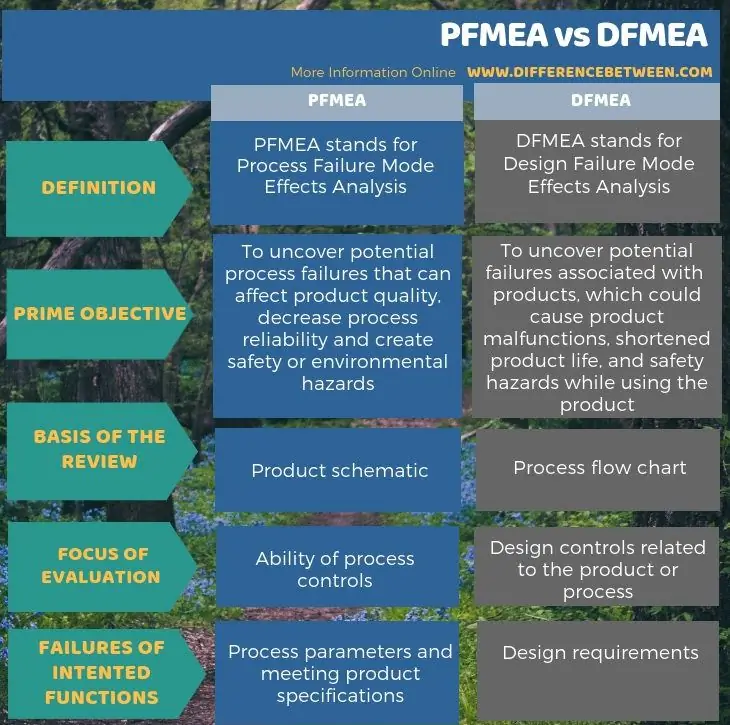
Резюме - PFMEA и DFMEA
Ключевое различие между PFMEA и DFMEA заключается в том, что PFMEA помогает анализировать потенциальные сбои конкретного процесса на уровне эксплуатации, тогда как DFMEA помогает анализировать потенциальные сбои конструкции продукта на уровне проектирования и разработки. Более того, эти методологии снизят производственные затраты, а также снизят возможные сбои при запуске продукта.